Town Hall Heating Upgrade
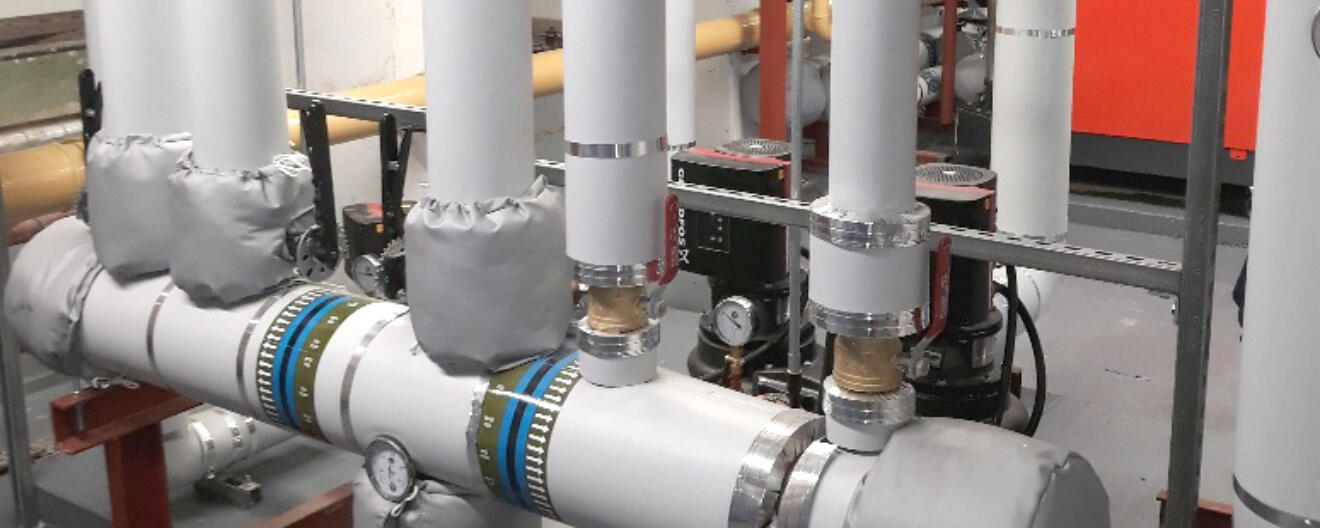
- Removal of three inefficient boilers, flues and pipe work
- Development of an asbestos management plan
- Asbestos containment
- Design of freestanding fixtures and brackets
- Installation of a combined heat and power (CHP) unit
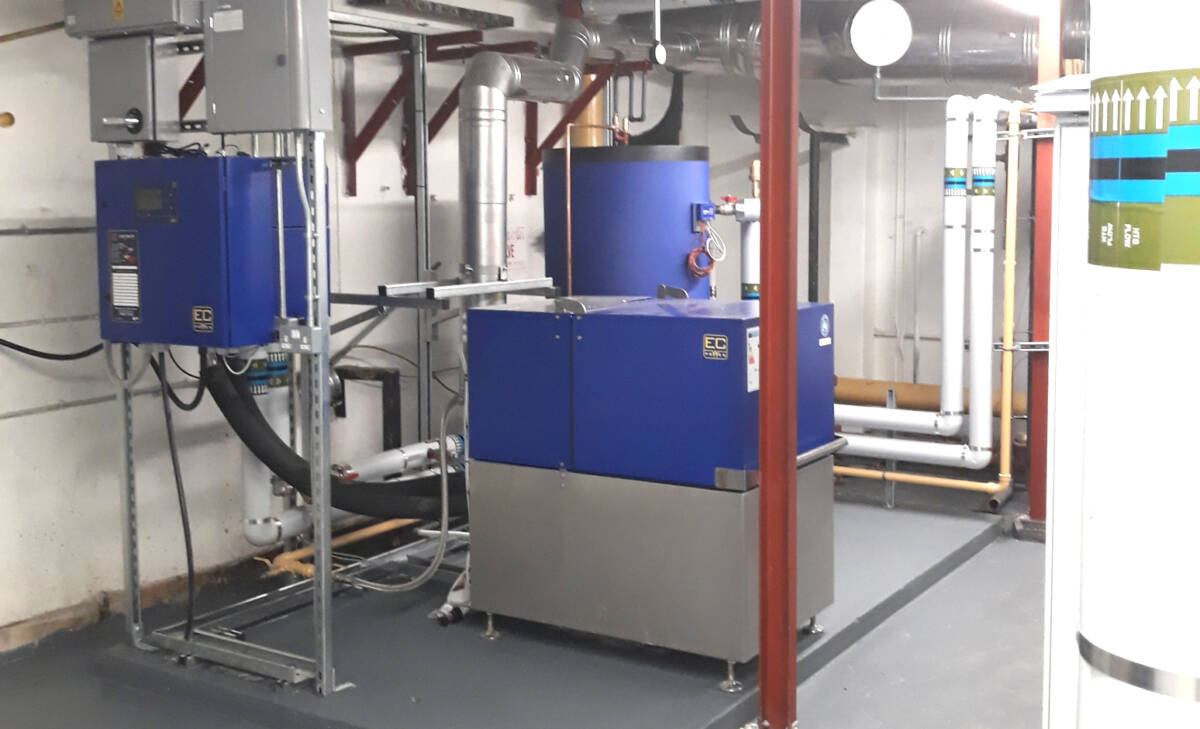
Based in the heart of Walthamstow, East London, Waltham Forest Town Hall is a Grade II Listed building that has served the local community since 1942.
As part of Waltham Forest Council’s plans to become a net-zero borough by 2030, the local authority made the decision to replace the Town Hall’s boiler and heating system in January 2018. A more reliable, efficient system would help to reduce the building’s carbon footprint while keeping employees and visitors warm.
With a view to completing the project by August 2018, the Council tasked Aston Group with the removal of three Kayanson 850Kw boilers – one of which had already been decommissioned and the other two had started to fail – along with the associated pipework and flues.
The Challenge
Working closely with Waltham Forest Council, Aston Group’s Gas Team developed a plan to efficiently remove and replace the Kayanson boilers, pumps and associated pipework with minimal disruption to employees.
At the start of the project, however, it was discovered that the plant room was subject to a prohibition notice. Large amounts of asbestos were on the floor around the boilers and pumps, posing a significant risk to health. As a result, only Aston Group’s Management team could access the plant room in the early stages – and no one could access the room unsupervised.
The presence of asbestos also meant that brackets and fixings could not be attached to the walls and ceilings, which meant a bespoke system had to be developed for the installation of pipework.
The Solution
The Council appointed Aston Group as the principal contractor and our Health and Safety Manager, George Ghaly, quickly got to work. He developed detailed risk assessments and method statements before notifying the Health & Safety Executive (HSE) about the asbestos and our plans to manage the project.
As part of these plans, Aston Group outlined how it would work with specialist asbestos removal company Keltbray in the first phases of the project. The document also emphasised that air monitoring systems would be installed to keep teams safe, while explaining that everyone involved with the project had a responsibility to report any new discoveries of asbestos. In addition, large proportions of the works were scheduled to take place outside of normal working hours in order to comply with the Council’s noise restrictions.
The HSE eventually granted its approval for the project in the middle June 2018, which meant both teams had to work hard to meet the Council’s deadline at the end of August.
Donning coveralls and breathing apparatus, the Aston Group team initially marked all the pumps and associated plant and pipework to be cut out by Keltbray.
Keltbray then got to work. They removed the existing boilers, pipes and plant and added a new ceiling, which was designed to enclose an 18-inch void filled with asbestos flock. The new ceiling was sprayed with two-hour-rated fire paint, before air monitoring was carried out and clearance certificates provided, as per the risk assessments. Only then could Aston Group access the site and install the new heating system.
Once on site, we removed the existing pumps, along with flow-and-return pipework on the Plenum Heating circuit as it enters and leaves the plant room.
Existing flues were taken back to the chimney stack and a CCTV survey of the remaining chimney stack was carried out to check for obstructions.
We then supplied and installed a new FuranFlex thermo resin flue liner, suitable for the condensing boilers. This was installed from the roof above and fed down into the boiler room, where it was connected to the new boilers. This allowed the builders to make good around the new liner/flue connection at the chimney stack.
Our teams also designed and created a free-standing bracket system with rubber feet and supports in order to install pipe work and infrastructure without drilling into the asbestos.
In total, Aston Group supplied and installed:
- 2 Remeha Gas 610 ECO PRO Condensing Boilers and Nabic safety valves
- A selection of Grundfos pumps
- An XRGI CHP to supplement the heating return circuits
- New gas safety valves
- A Flamco FC DAC 150 F air and dirt separator and a new 25-litre dosing pot
- BMS control circuits utilising the existing control panel.
The Results
The discovery of the asbestos meant that the project was slightly delayed. However, working closely alongside Keltbray, Aston Group completed the whole project just a few weeks behind schedule, in October 2018.
“Aston Group successfully delivered what I considered to be one of the most problematic boiler house projects I have ever undertaken.
“Although the works themselves were quite straightforward – and within Aston Group’s expertise – the project was not without its problems.
“It involved a short programme period of 12 weeks and restricted access within a fully occupied 3‑storey, Grade II-Listed building, which houses the Council’s central offices. Due to noise restrictions during working hours, the project involved out of hours and weekend working. And that’s without mentioning the disastrous discovery of asbestos within the boiler room!
“Following sleepless nights, many discussions, lots of stress, plus an extensive amount of collaborative work, we managed to deliver a successful project with the support of Aston Group. My personal thanks go to Gary Foley, Phil Ford, Martin Barlow and Alan Thomas for their input.”
Lead Project Consultant, Town Hall Boiler House Project, formerly of the Waltham Forest, Capital Delivery Team