High Rise Tower Block Boiler Upgrade
Improvements to the heating and hot water supply
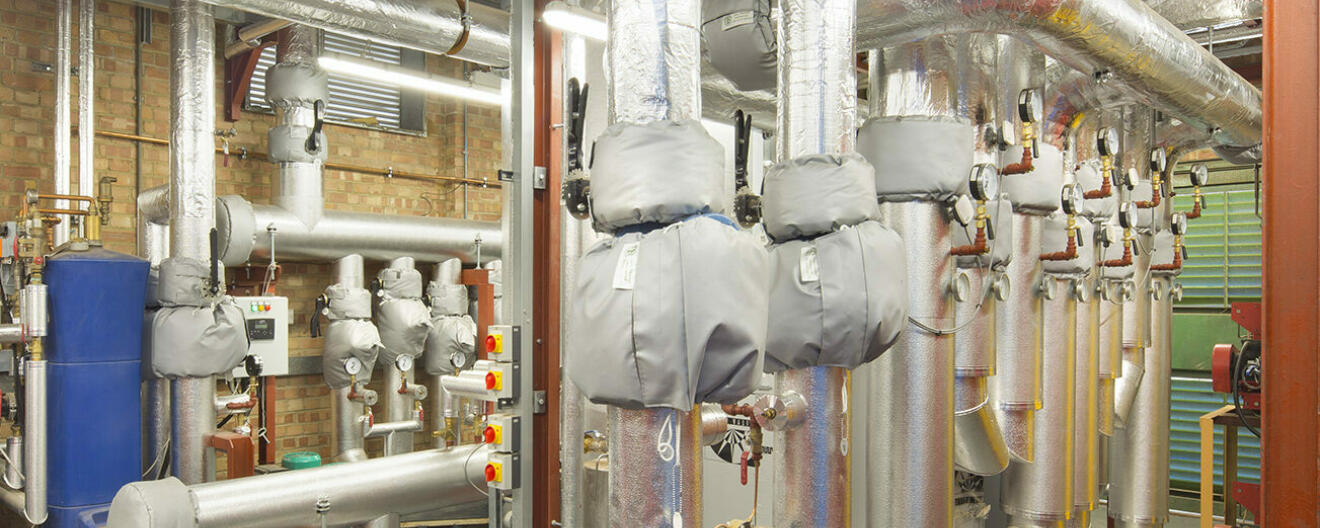
- Removal of existing CHP plant, pumps, controls and pipework system
- Removal of existing secondary heating distribution system
- Installation of a new heat exchangers, buffer vessel, pumps, controls and pipework system
- Installation of new primary heating distribution system
- Installation of new heating interface units providing radiator heating and instantaneous hot water to 232 residential units
- Development of a comprehensive Method of Working document, taking the effects of Brexit and Covid-19 into account
Located in the London Borough of Waltham Forest, John Walsh and Fred Wigg Towers are 17 storeys tall and home to 232 individual flats. Erected in 1965, the local council has been engaged in updating and improving a number of facilities at high rises like these throughout the borough in recent years, improving safety and well-being for residents.
With the boiler plant and pipework shared by the two towers deteriorating and starting to fail, the local authority grew concerned about the reliability of the system and potential safety issues as leaks became more common.
Having already engaged Aston Group on several occasions, Waltham Forest Council approached us in September 2019 with a request to design and install a boiler and plant room upgrade while we also upgraded the lifts in both blocks.
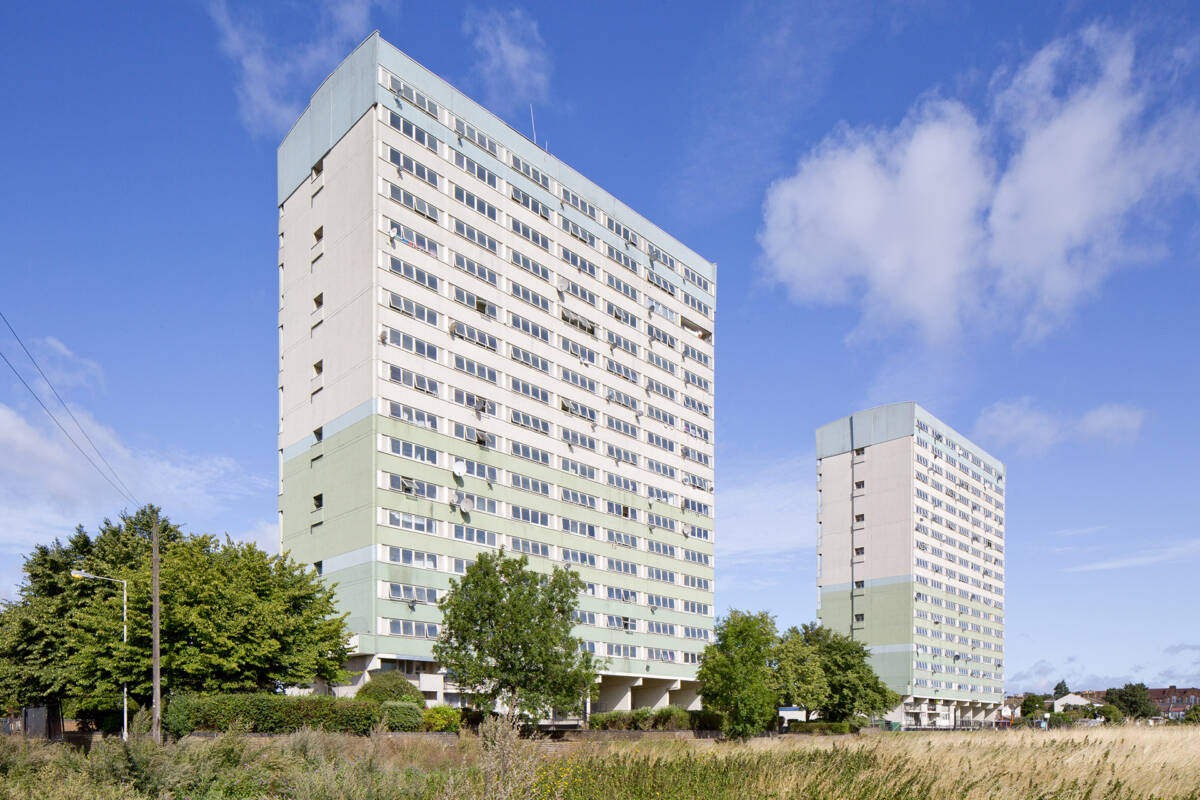
The Challenge
From the outset, the biggest obstacle related to resident well-being. Not only were the lifts out of action while work was undertaken on both projects, but it was essential that any negative effect on heating and hot water was minimised.
Once the system had been designed, it also became apparent that supply chain disruption could affect the delivery of materials and equipment, following Britain’s departure from the European Union. This had to be factored into the planning process.
In addition, once the upgrade plan had been approved by Waltham Forest Council, the Covid-19 pandemic began. Plans had to be adjusted for both worker and resident safety, resulting in the reduction of the size of our teams and the introduction of new Health & Safety measures.
The Solution
Our highly trained team worked closely with Waltham Forest Council to develop a comprehensive system of works, detailing timelines and the potential impact on residents. We meticulously planned the project to reduce any negative effects for residents, choosing to complete the works over the summer months while central heating was not needed.
Once the plan was approved, we held two Q&A sessions with residents, during which they were invited to raise any concerns. These could be factored back into the project and timelines.
This was followed by a monthly working group, which was attended by key stakeholders and resident representatives. A WhatsApp Group was also set up to facilitate smooth communication and the rapid resolution of any issues.
A key consideration before starting work on the replacement of the boiler plant was resident access to hot water; although heating was not needed over summer, hot water was essential. As such, our teams checked that each individual flat’s electric immersion heater was functioning correctly. If not, it was replaced.
Once complete, we drained the heating system in both blocks and the shared plant room. From there, we removed the riser pipework from both blocks, as well as the lateral pipework from the riser cupboard to the lift lobbies.
New tees were then added to the remaining lateral pipes, which allowed new valves to be fitted. Two valves would serve new lateral pipes while another two would be used to close the old system. This would allow us to remove existing lateral pipes from each floor once the new system was in place.
This was also completed on the lower ground floor, which enabled the team to connect new plant room pipes to new valves, which then connected back to existing underground pipework.
Once this was installed, new riser pipework sleeving and fire stopping were fed through each floor slab and connected onto the new tee and valve arrangements in each lift lobby.
All sections were hydraulically pressure-tested, chemically flushed and cleaned. Once complete, we reinstated both towers’ heating and primary hot water supply before the end of September – a time frame of fewer than 5 weeks.
While this was happening, our groundworker dug two trenches to and from both blocks, keeping all aspects of the project moving. We installed new pre-insulated steel pipes, electric-welded, tested and flushed, then back-filled and Tarmac/concrete-finished both trenches.
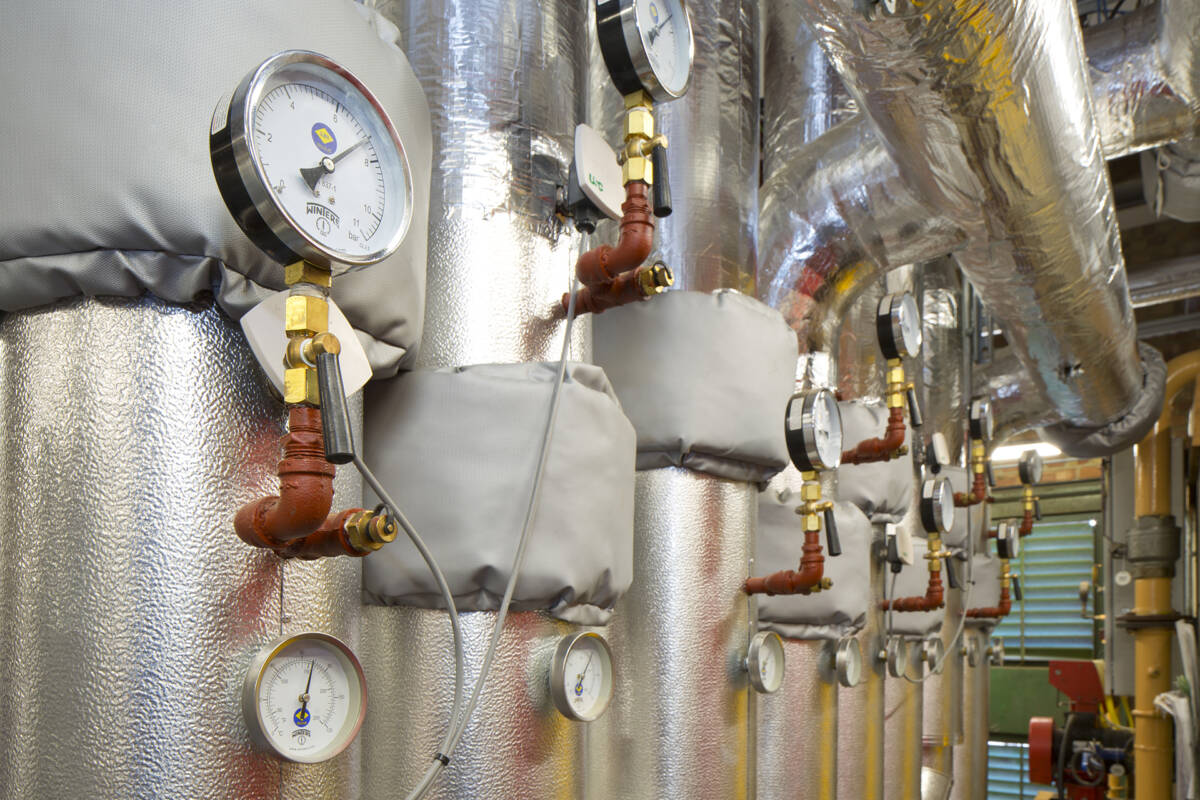
In the boiler plant room, we also installed two plate heat exchangers (PHE), a 4,000 litre buffer vessel and new boiler shunt pumps. These connected to the new tees and valves, which were installed in the shutdown.
Pumps were used from the buffer vessel through the PHE. From the PHE, pipework served individual twin pumps, which serviced both blocks. We then connected these pipes to the installed underground pipework.
Once the new pumps and degasser and pressurisation units were wired and commissioned, we used flushing points to circulate fluid around the new buffer, PHE and link pipes at the bottom of each riser to test them.
When we had the correct temperature, we opened the valves to the new pipework and closed the old, switching supply to the new system without any downtime or impact to the residents.
Once the main infrastructure was in place, our teams started work in the flats. Working on a floor at a time, our Resident Liaison Officer contacted each property to arrange a date and time for installation for all 232 flats.
At the agreed time, our team installed new radiators and a Heat Interface Unit (HIU) in each home. Boiler plant hot water is pumped to the flat and heats the individual HIU as needed.
There were a number of benefits to this, not least from a safety perspective; rather than hot water being pumped at high pressure from the boiler room to each flat, residents now have their own heating system. Not only that, but it allows all flats to pay for the energy they use, rather than a share of the whole building’s energy consumption.
Once each floor was complete, we closed the valves installed during the first shutdown and drained the old lateral pipes, before cutting them out and plugging the two valves. Once again, there was no downtime for the residents.
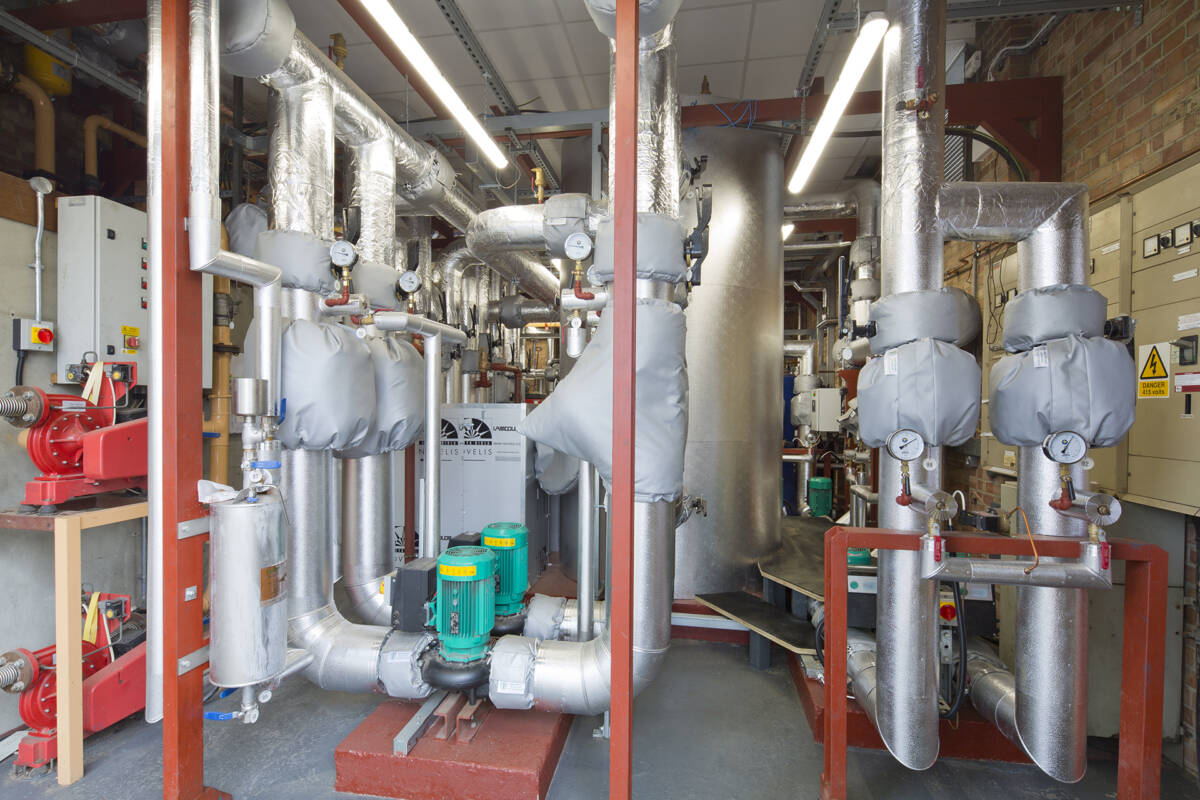
The Results
The new boiler plant and heating systems were completed with no disruption ahead of schedule in September, prior to commencement of the heating season. Plus, residents now have more control over their own central heating and hot water systems, while also being safer.
Waltham Forest Council was delighted by the project being delivered ahead of schedule, with no system downtime. And, thanks to our planning process, they saved 35% on the cost of materials because of inflationary increases during the course of the project.